A Wilier Triestina márka termékmenedzsere, Claudia Salomonival és mérnöke, Marco Genovese-zel beszélgettünk.
A kerékpártervezés modern kihívásai
Manapság bárki, aki biciklit akar vásárolni, akár az interneten vagy a helyi bringaboltban, biztosan hallott vagy olvasott már legalább az egyik kifejezésről a következők közül: merevebb, könnyebb, aerodinamikusabb.
De minden cég főhadiszállásán ott lebeg egy állandó cél; a gyártás költséghatékonysága. Ebben rejlik a fő kihívás egy nagy kerékpárgyártó cég mérnöki csapata számára.

Claudio Salomoni, ezek a fő célok hogyan egyeztethetőek össze a modern kerékpárgyártásban a gyártási kiadások ellenőrzésével?
A költségek kontrollálása kétségtelenül fontos, de ez csak egy, a számos szempont közül, amelyet figyelembe kell vennünk a munkánk során. Mivel mi egy kisebb cég vagyunk, számunkra ez még fontosabb, mivel sokszor mi nem élvezzük azokat a nagy termelési számokból adódó előnyöket, amelyeket a nagy gyártók igen.
Ha már itt tartunk, mikor mi elkezdünk dolgozni egy új biciklin, akkor mindig van egy álomkép – maga az ötlet és hogy milyennek is kéne lennie ennek az álom bringának. Innen pedig visszalépünk a valóságba, rátérünk a kompromisszumokra, ahol az eredeti ötlet talán túl drágának bizonyul, egy új technológia kifejlesztése túl sokba kerülne, vagy egy alapanyagról kiderül, hogy nem megfelelő. Tehát ez az egész arról szól, hogy hol kell visszavenni és hol nem.
Jó persze, megépítheted A BRINGÁT, de az akár kétszer annyiba is kerülhet vagy még annál is többe. Lehet, hogy eladsz pár darabot, de a céget nem fogod megmenteni.
Ez sok szempontból igaz az összes többi gyártóra, az iparág felsőbb szintjein is. Az igazat megvallva, mind olyan kerékpárokat gyártunk, amelyek hasonló jellegűek. Mégis lesznek olyan emberek, akik bizonyos márkákért többet hajlandóak fizetni, másokért kevesebbet.
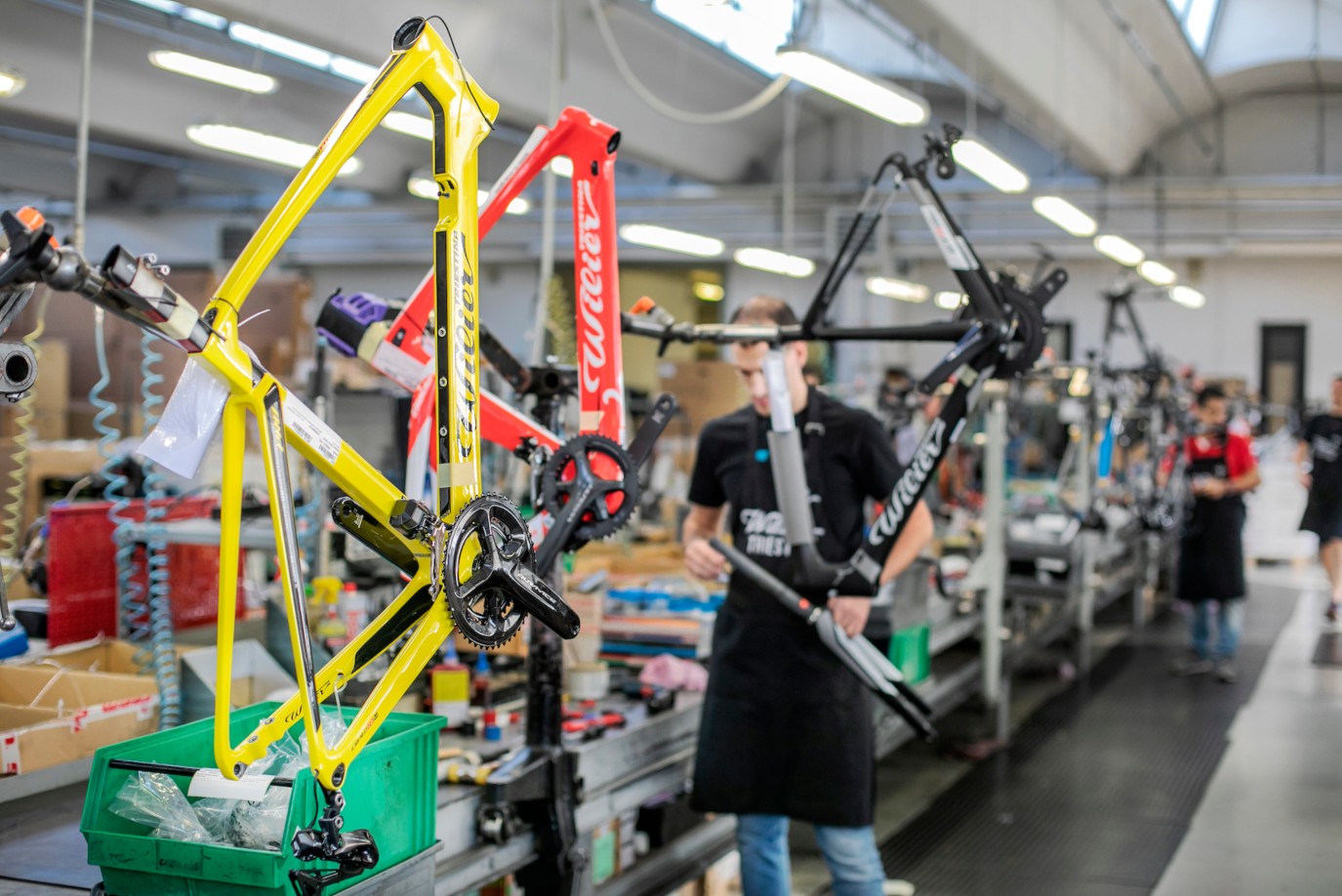
Ha visszanézel, régen is így működött ez. Mindenki Columbus vázat használt és nem sok különbség volt a különböző bringák között.
Említetted a merevséget korábban és azt kell hogy mondjam, a Wiliernél ez valóban egy fontos tényező, de azért nem erőltetjük minden áron. A súly-merevség arány egy fontos szám szerintem. Mi a megfelelő arányú merevségben hiszünk, mivel ez kényelmesebb tekerést eredményez.
A másik dolog, aminek hívei vagyunk, a kiegyensúlyozott dizájn, amely annyit takar, hogy a különböző méretű vázak esetében a csövek általános hosszúsága és szélessége kissé eltérő. A módszer kiindulási pontja alapvetően a közepes méretű váz, mivel ez a standard méret. Ehhez mérten igazítjuk a többit. Ezzel a módszerrel az XXS és az XXL vázak a közepes méretűekhez hasonlóan megtartják a merevségüket, csupán a vonatkozó arányaik fognak kissé eltérni.
Az út a karbonig
A karbon jelenleg minden nagyobb gyártó alapanyag választása a közép árkategóriánál kezdődő bringák esetében és szó szerint mindenhol ott van. A skála alján mindig megtalálható az alumínium és úgy tűnik, a magasabb kategóriás bringáknál is újra számításba jön a legújabb gyártási folyamatoknak köszönhetően. Gondoljunk csak a hydroforming eljárásra vagy az új hegesztési technikákra, amelyek segítségével a gyártók olyan vázakat készíthetnek, amelyek felveszik a versenyt a karbonból készülő társaikkal. Jó példa erre a többszörös világbajnok Peter Sagan, aki alumínium bringán tekerte le idén a Down Under Tour-t Ausztráliában.
A többi alapanyagot tekintve, az acél használata inkább az egyedi kerékpárgyártók körére korlátozódik, míg a titánium a nagy költségvetéssel rendelkező szakértők igényeit is kielégíti.
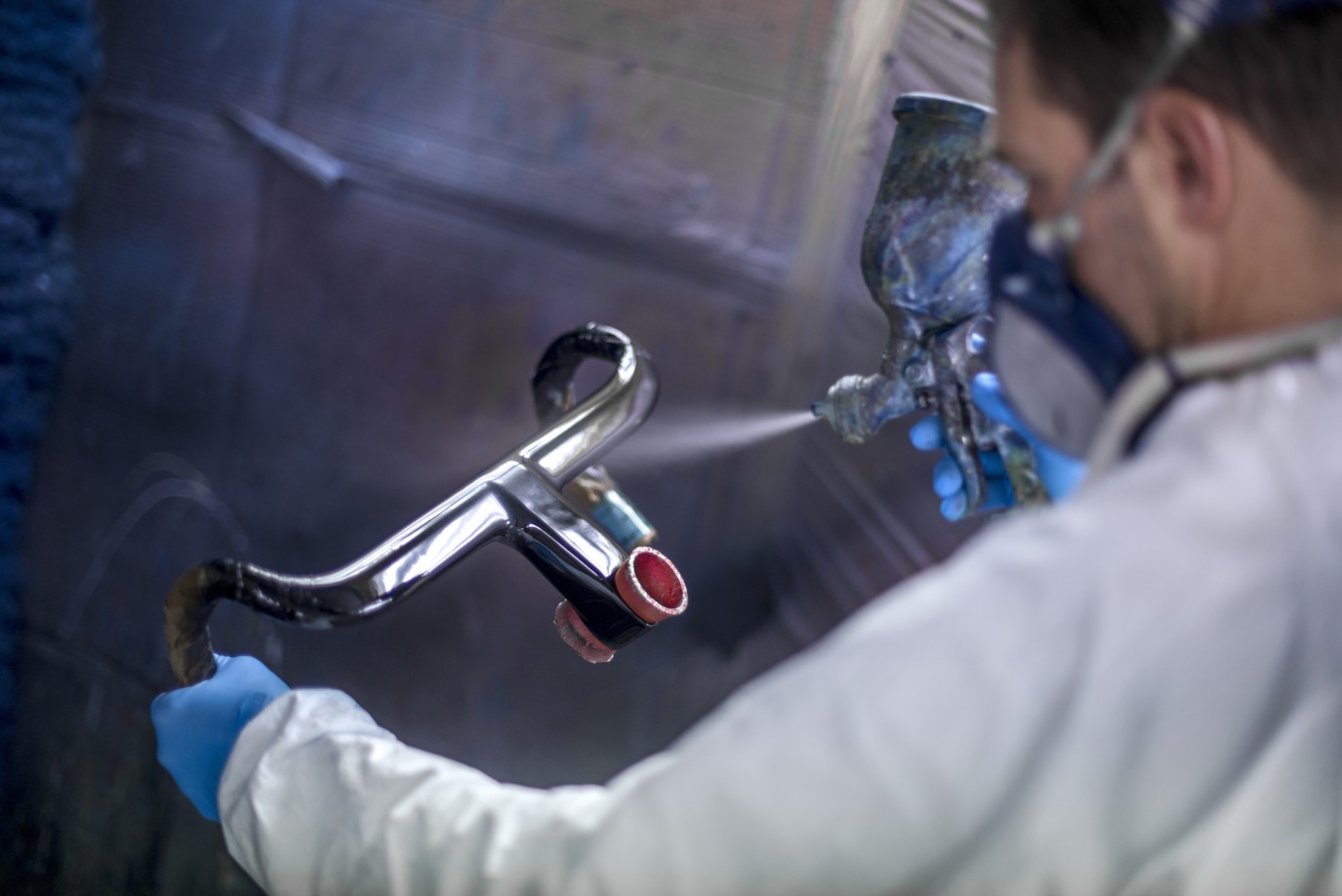
Hogy látjátok a piac alakulását a következő pár évben az új kompozit anyagok tekintetében?
Marco Genovese: Nagyon jó kérdés. Őszintén szólva én azt látom, hogy a legutóbbi fejlesztések csupán technológiai jellegűek, szóval inkább a gyártási technológiák fejlődésén alapulnak, mint sem az új anyagokon. A kompozit anyagok terén a fejlesztések eddig még elég lassúnak mondhatóak. A karbonszálakkal ugyanez a helyzet. Néha látunk új adalékokat az összetevők terén, de a sajátosságok még mindig nagyjából ugyanazok.
Claudio Salomoni: Ha a kerékpáripart nézed, az egész végül is az acéllal indult, aztán mindenki váltott az alumíniumra, most pedig mindenki karbont és műgyantát használ. 2011-ben elkezdtünk használni egy kissé eltérő kompozitot, ami nem csupán karbon volt, de egy fajta karbonszálba oltott ömledék, amely növelte az ellenállást az ütésekkel szemben és fejlesztette a tompítási képességet, ami ennek köszönhetően kényelmesebb tekerést eredményezett. Szerintem ez a jövő. Abban viszont nem vagyok biztos, hogy ez melyik alapanyagot vagy anyagokat érinti majd.
Ez egy érdekes megközelítés, mivel ahogy mi látjuk a dolgokat, a karbon egyik fontos hátránya az ellenálló képessége. Ha egy amatőr bringás kerékpárja az aszfalton landol, az a váz megrongálódását okozhatja.
Claudio Salomoni: Abszolút. Pontosan emiatt dolgozik az egész iparág azon, hogy ezen változtassanak azáltal, hogy új kompozitokat adnak a karbon szálakhoz és a műgyantához. Ez pedig a nanoszálas megoldásokhoz hasonlóan fog kinézni, amely olyan, mintha apró buborékok lennének a rétegek között és ezek segítenek az ütések keltette rázkódás tompításában.
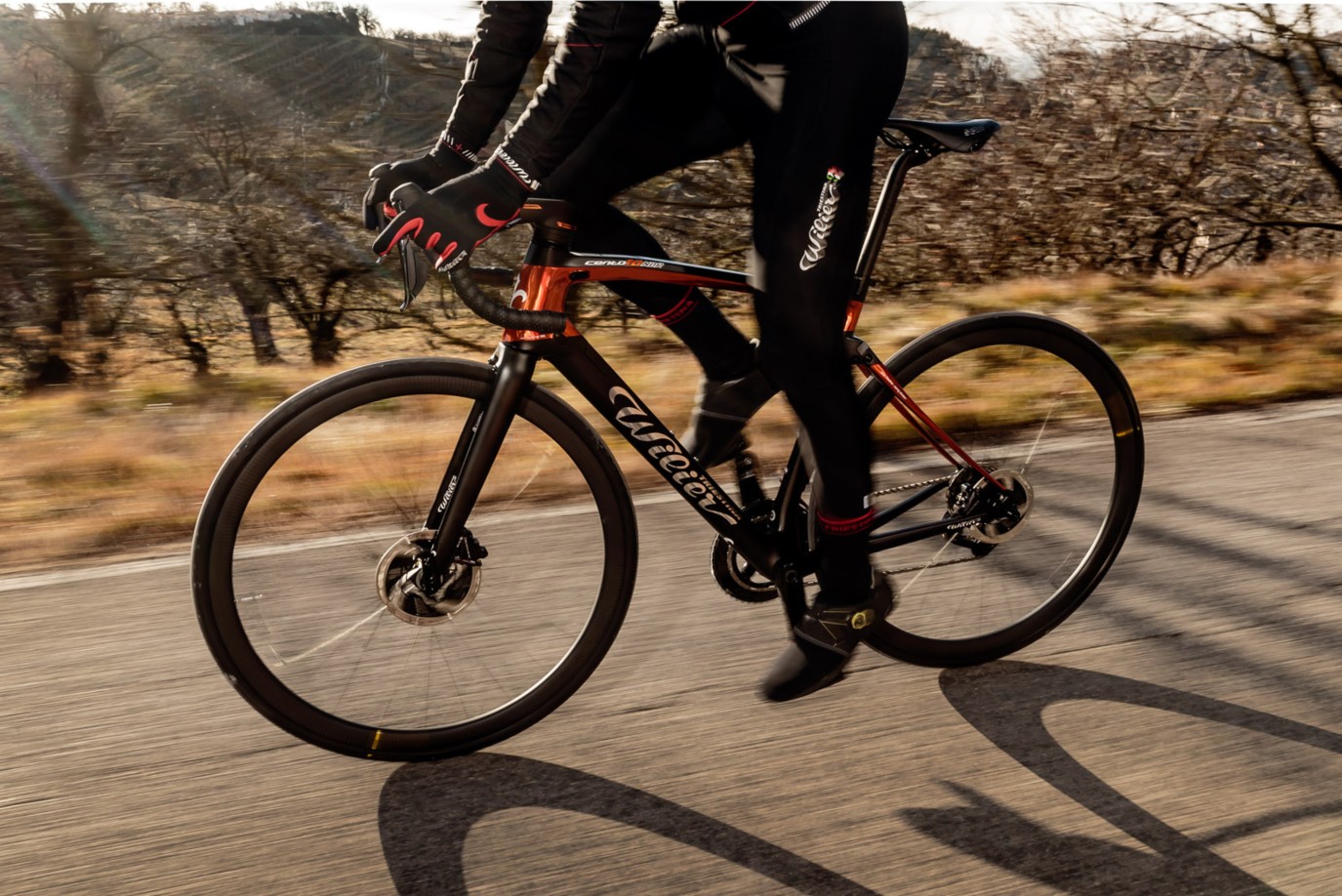
Jelenleg ezekkel az úgynevezett egzotikus alapanyagokkal foglalkozunk, mint a nanocellulóz és társai. Ázsiai partnereinkkel vizsgáljuk ezeknek a lehetőségét.
És mi a helyzet a legújabb kerékpárváz gyártási trendekkel kapcsolatban?
Claudio Salomoni: Ki tudja?!
Ha te igen, akkor kérlek oszd meg velem is (mosolyog). Komolyra fordítva a szót, amit tudok biztosan, hogy rengeteg szó esik a legújabb 3D nyomtatás vívmányairól, amelyek a jövőben hasznosak lehetnek a kerékpárgyártás számára.
Mellékesen jegyezzük meg, hogy Marco díjat nyert az #Eurobike-on miután egy olyan MTB kerékpárt tervezett, amely újrahasznosított műanyagokból készült. Szóval szerintem a 3D-s trendet mindenképp érdemes figyelemmel kísérni.
Szintén ide kapcsolódik, hogy sokak szerint lehetséges a karbonnyomtatás is. Ma ez még nem egy működő dolog, de egyértelműen lehetőségnek számít. A 3D nyomtatás legnagyobb előnye minden gyártó számára, a jelentős gyártási költség csökkenés lenne, mivel meg lehetne spórolni az öntőforma-készítés drága, manuális részét. Még senkinek sem sikerült ezt kiviteleznie, mivel az ötlet még mindig csak a laborokban létezik, de ez mindenképp egy lehetőség a jövőre nézve.
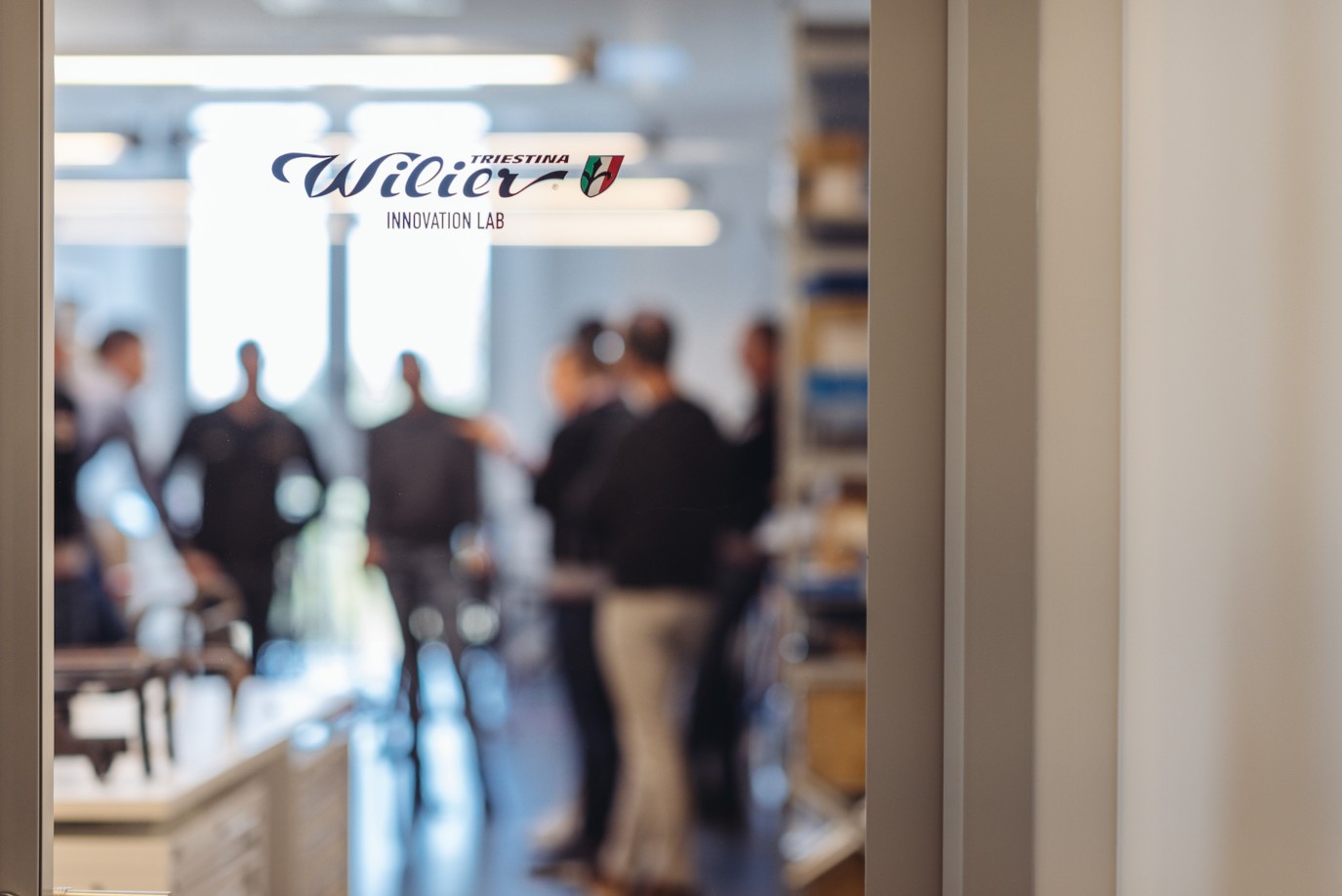
Ezzel pedig elérkezünk egy másik kérdéshez: a költséges kutatási és fejlesztési folyamatokkal kapcsolatban általában hogyan működtök együtt az ázsiai partnereitekkel?
Claudio Salomoni: Ez alapvetően egy kétirányú folyamat, amelyben az ötletek egy része tőlük jön, a másik pedig tőlünk. Ez épp az adott napi információcserétől függ. Nem úgy működik, hogy leadjuk a rendelést aztán várunk, amíg megérkezik az áru.